The TUDOR Manufacture is the first industrial facility fully dedicated to the TUDOR watchmaking company in its nearly 100-year history. Located in Le Locle, Switzerland, this is where every single TUDOR watch is assembled and fully tested to TUDOR’s superior standards, with some models in the range Master Chronometer-certified here, too. This new state-of-the-art facility, bringing together the traditional know-how of watchmakers with the best in production management technologies and automated testing systems, was completed in 2021 after three years of construction. All decked out in TUDOR red, the manufacture spans over five levels totaling 5,500 square meters and is physically and visually connected to the neighboring Kenissi Manufacture, the TUDOR movement production facility. With Kenissi and a network of TUDOR-owned affiliates, the brand has been able to integrate the development and production of high-performance mechanical calibres. As a consequence, TUDOR now fully masters the manufacturing of strategic components and can guarantee their quality.
HISTORY
The TUDOR Manufacture is now a fixture in the bucolic town of Le Locle, located in the Jura Mountains on the northwesternmost border with France in the Canton of Neuchâtel. While the town plays host to a relatively small population of 10,000, the importance of Le Locle in the watchmaking industry cannot be understated. Together with the neighboring town of La Chaux-de-Fonds, the region has been honored as a UNESCO World Heritage site since 2009. Initially an important agricultural region, the area became one of the main hubs of watchmaking in Switzerland as early as the 17th century. After fires destroyed much of the town, it was rebuilt to service the growing timekeeping industry, with residential housing mixed with workshops along parallel streets to maximize efficiency.
The construction of the TUDOR Manufacture started in 2018, with the objective of moving the assembly operations of Montres TUDOR SA from Geneva closer to its affiliates and suppliers in the Jura mountains. The Group owned undeveloped industrial land in Le Locle next to a Rolex facility inaugurated in 1970, making it the perfect site for the TUDOR Manufacture. The signature TUDOR red building was fully completed in 2021 and officially inaugurated in March of 2023 during Switzerland’s premier watchmaking tradeshow, Watches and Wonders.
BREAKING DOWN THE MANUFACTURE
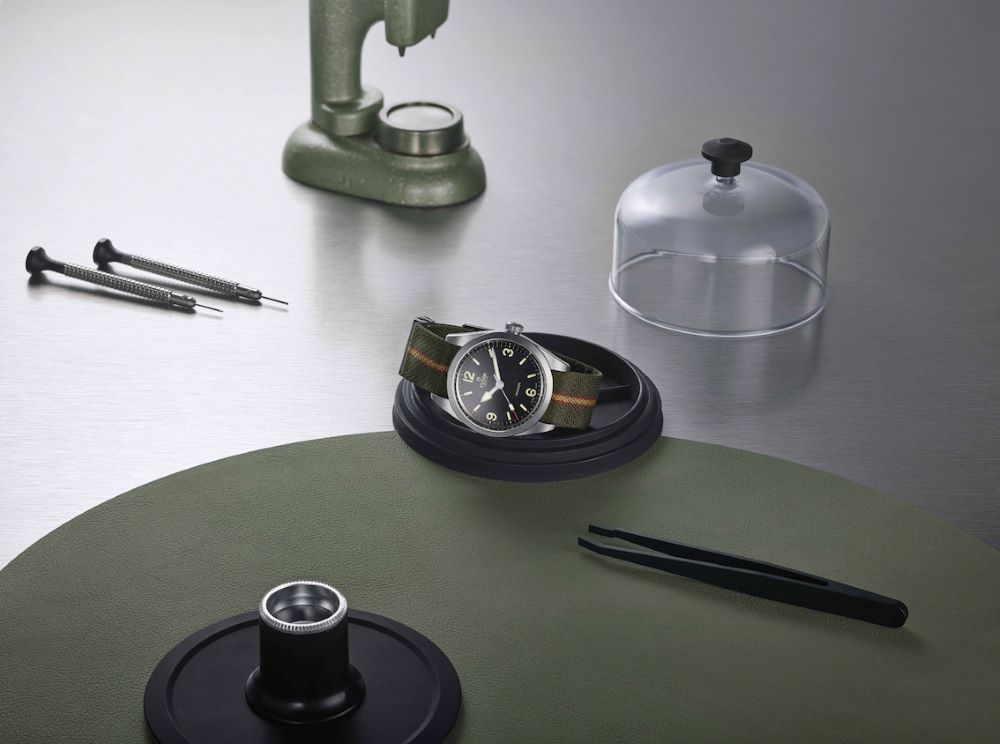
The manufacturer is home to a team of 150, all working hard in numerous functions to produce the most reliable and robust watches possible. A core tenet of TUDOR is to ensure that its watches offer the ultimate in value to the consumer. To do this, it has perfected a unique blend of automated production technology with the technical know-how of highly skilled watchmakers. The most cutting-edge technology available, in-building logistics systems, and automated testing are leveraged to offer the best possible watch at the best possible price to the consumer.
Kenissi – TUDOR’s movement production arm
Many of TUDOR’s watches feature a Manufacture Calibre, which is developed and assembled at Kenissi, TUDOR’s movement production arm. In fact, the buildings are conjoined. Everything from research and development to final assembly takes place here for TUDOR’s Manufacture Calibres. In addition to TUDOR’s own demands, Kenissi was created in 2010 to develop its industrial production capacity for high-performance mechanical movements. To this end, the brand brought together a group of experts and presented an initial calibre at Baselworld in 2015. The first client of Kenissi besides TUDOR itself was Breitling, and as its business developed, Kenissi formed an industrial alliance with Chanel in 2018. Today, the clients of Kenissi also include, Norqain, Fortis, TAG Heuer, Bell & Ross, and Ultramarine.
The Kenissi production line exemplifies TUDOR’s commitment to leveraging the power of combining the most advanced tech with the expertise of the human hand. First, the mainplate is mounted on an insert of appropriate diameter embedded with an RFID-TAG. The inserts are put on a shuttle device and enter the assembly line at the first workstation. The RFID-Tag guarantees the correct routing of the soon-to-be calibre. This tech assures the full traceability of the calibre and collects all the assembly data in order to improve product quality, productivity, and assembly processes through big data analysis. After having passed the first fully automated test cycle on the assembly line, all movements are sent to the COSC, the Official Swiss Chronometer Testing Institute. Then it’s off to TUDOR to find a home in a watch.
Assembly
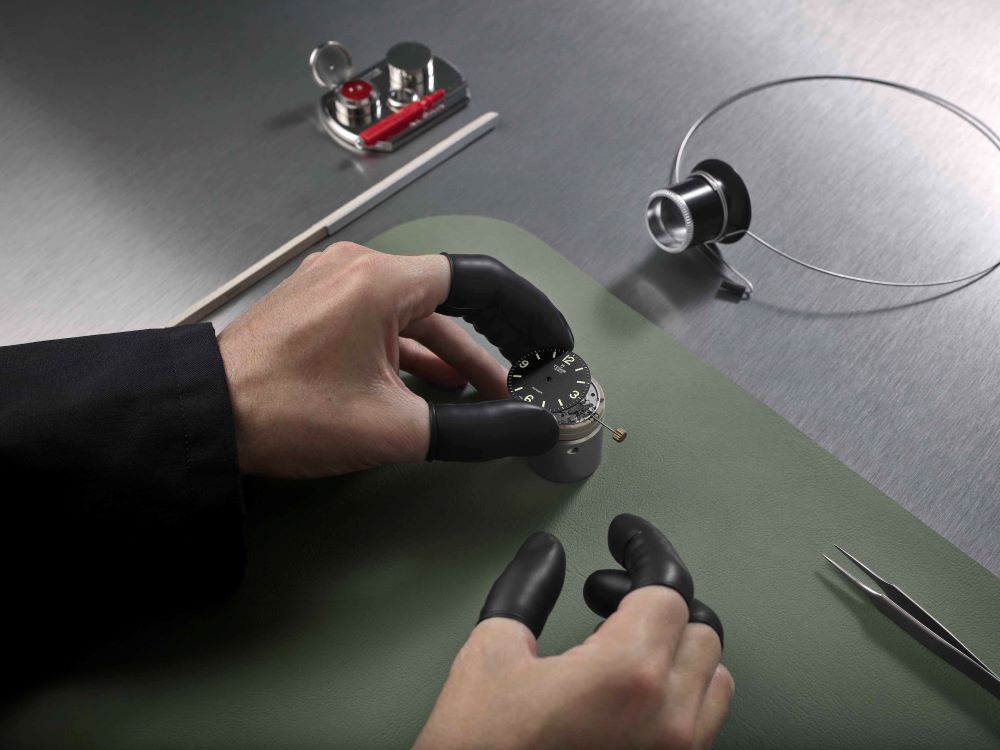
The first technological advantage a watchmaker has is a constant positive pressure environment throughout the workshop. In order to mitigate the opportunity for dust ingress into watches and machinery, the TUDOR Manufacture’s HVAC system, located in the basement, plays a crucial role. The system creates a continuous flow of air from the ceiling to the floor so that dust is kept from floating around the workshop.
To deliver value to the end user, TUDOR doesn’t maintain a stock of assembled watches. Every watch produced is destined to shortly be on a client’s wrist. This means every watch is closely tracked and data can be used to improve efficiency. It also means that the workshop needs to be very flexible, agile and versatile. Watchmakers must master every assembly operation through cross-training. TUDOR achieves this through autonomous cells of four watchmakers that are trained in every discipline of the process. Each bench is laid out in the same way, from its machinery to the contents and organization of its drawers. This is meant to provide a homogenous and ergonomic work environment, optimizing operations and efficiency. The team members of a cell always work together. They train with their cell before being fully operational to create team spirit and improve efficiency. Within the cells, each team member is capable of assembling any reference in the TUDOR collection. One cell covers the three following operations in chronological order: dial-fitting, hand-fitting, and casing.
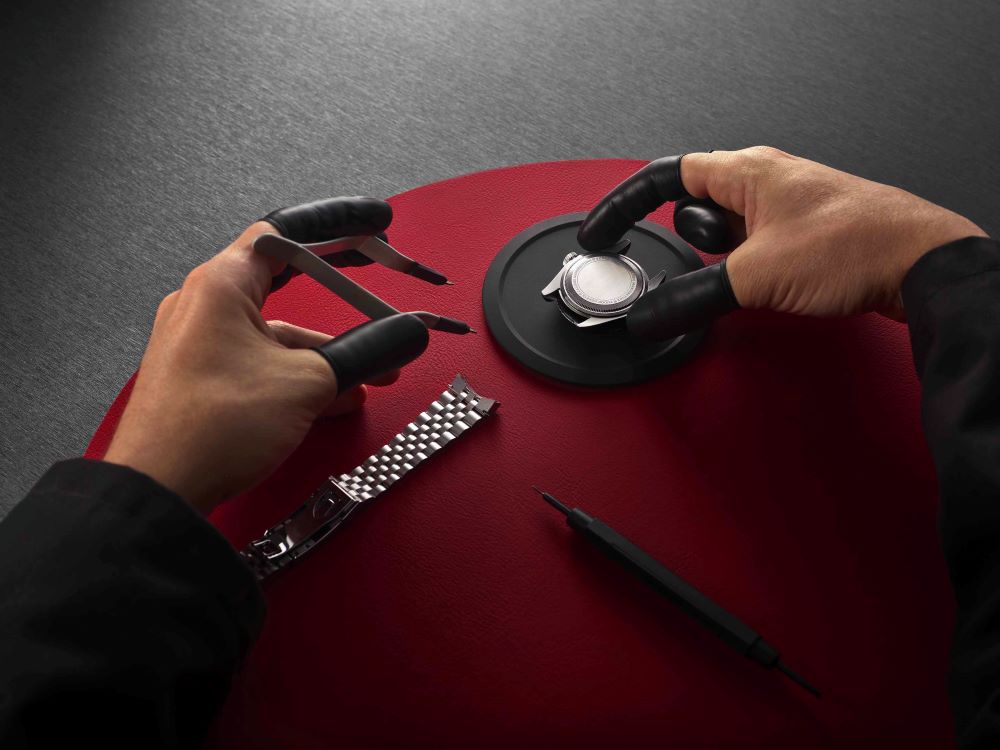
Testing
All TUDOR watches are tested at the TUDOR Manufacture. Every model passes the TUDOR Performance Control, meaning the watch, fully assembled, meets (-2/+4) seconds precision per day if it is equipped with a Manufacture Calibre, (-4/+6) with other calibres. In addition, all watches are tested for waterproofness in hyperbaric water tanks. Some models in the TUDOR range meet the METAS standard, which is much more exacting. Eventually, every TUDOR watch will be Master Chronometer-certified by METAS.
METAS’ Master Chronometer certification is comprehensive and covers the main functional characteristics of a watch, including precision, resistance to magnetic fields, waterproofness, and power reserve. Its standards are incredibly high, starting with precision. To qualify, a watch must be able to function within a 5-second range of variation each day (0/+5), that is to say, 5 seconds less than the Official Swiss Chronometer Testing Institute (COSC) (-4/+6) and a second less than TUDOR’s internal standard (-2/+4), which is applied to the brand’s models with a Manufacture Calibre. The certification also guarantees the timekeeping accuracy of a watch subjected to magnetic fields of 15,000 gauss. Finally, it also guarantees that the waterproofness claimed by the manufacturer conforms with the International Organization for Standardization (ISO) standards, as does the power reserve. It should also be noted that two prerequisites are necessary before the certification can be obtained: Swiss manufacturing must conform with the criteria of Swiss Made, and the movement must be certified by the Official Swiss Chronometer Testing Institute (COSC).
TUDOR IS BORN TO DARE
The TUDOR signature is Born To Dare. It reflects both the history of the brand and what it stands for today. It tells the adventures of individuals who have achieved the extraordinary on land, on ice, in the air or underwater, with a TUDOR watch on their wrists. It also refers to the vision of Hans Wilsdorf, the founder of TUDOR, who manufactured TUDOR watches to withstand the most extreme conditions, watches made for the most daring lifestyles. Finally, it is testimony to TUDOR’s pioneering approach to watchmaking, which has helped to make it what it is today. At the cutting edge of the watchmaking industry, the brand’s innovations are now essential benchmarks. The TUDOR Born To Dare spirit is supported globally by high-profile ambassadors — including David Beckham, Jay Chou, and the All Blacks — whose achievements directly result from a daring approach to life.